July 23rd 2025
Advancing Performance: Modern Machining Methods for Cylinder Heads
Advancing Performance: Modern Machining Methods for Cylinder Heads
MEC CNC Webinar Delivers Critical Insights on Precision Machining for High-Performance Engines
In a recent episode of the Race Industry Now webinar series, Anthony Usher, President of MEC CNC, and Chuck Lynch, Vice President of Technical Service at the Automotive Engine Rebuilders Association (AERA), delivered an in-depth discussion on the latest machining innovations for cylinder heads. The session explored precision machining techniques, valve guide accuracy, valve seat preparation, and gasket surface finishing—all essential elements for maximizing performance, reliability, and longevity in racing engines.
The Importance of Precision in Cylinder Head Machining
The webinar emphasized that every high-performance engine begins with accurate reference points, particularly in the valve guides. Lynch explained how valve guides serve as the critical datum point for valve seat machining, influencing combustion sealing, heat transfer, and component longevity.
Usher highlighted advancements in valve guide honing machines that achieve tighter tolerances and superior surface finishes, enabling reduced valve-to-guide clearance for better valve control, improved airflow, and enhanced durability.
Valve Seats: Where Power and Reliability Meet
Precision valve seat machining is crucial for sealing combustion chambers and ensuring efficient heat transfer. The speakers detailed multiple angle seat machining (3-angle, 5-angle, and even 7-angle profiles), which optimize airflow and performance while maintaining proper sealing.
They also addressed valve seat runout, a common cause of valve failure and head breakage. MEC CNC’s advanced tooling and piloting systems reduce side loading and chatter, minimizing runout and improving consistency.
Innovations in Tooling and Measurement
Modern machining challenges require rigid tooling, precise pilots, and advanced measurement techniques. Usher introduced new dual-opposed insert tooling systems that balance cutting forces, dramatically improving surface finish and seat concentricity.
The webinar also covered vacuum testing and concentricity gauges as complementary methods to ensure accurate valve seating. Lynch underscored that seat runout must never exceed valve stem-to-guide clearance, reinforcing the need for precision at every step.
Surface Finishing for Modern Gasket Technology
With the widespread adoption of MLS (Multi-Layer Steel) head gaskets, surface preparation has become more critical than ever. The discussion explained how surface roughness, flatness, and waviness affect gasket sealing under extreme conditions.
MEC CNC’s state-of-the-art surfacing machines, equipped with advanced spindle design and rigid fixturing, ensure gasket surfaces meet the strictest performance requirements, even for high-compression, high-boost racing engines.
Key Takeaways for Engine Builders
- Accurate valve guide machining is the foundation of reliable valve sealing.
- Honing vs. reaming—honing delivers straighter, rounder guides with superior surface finishes.
- Minimized valve seat runout reduces stress on valves and guides, preventing premature failures.
- Advanced tooling and pilots improve consistency, reduce chatter, and achieve better heat transfer.
- Modern gasket technology demands smoother, flatter surfaces for optimal sealing.
For more information, watch the full webinar here.
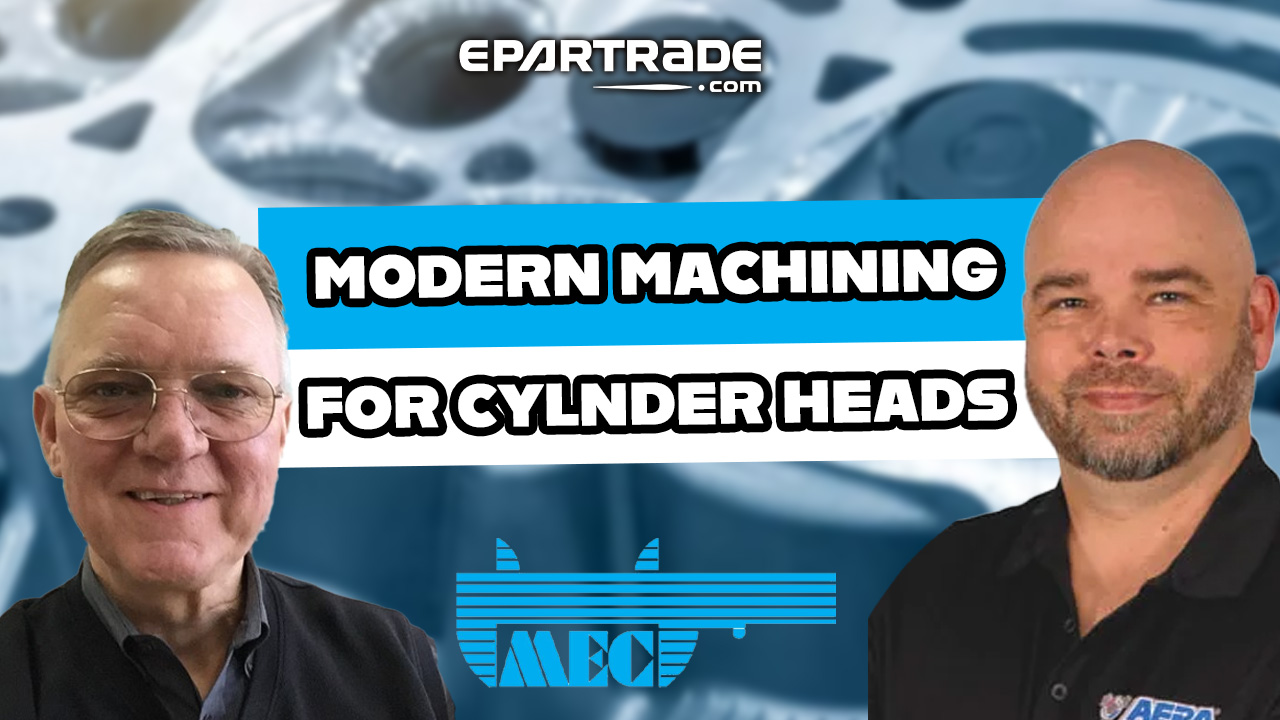