November 23rd 2022
Powertrain focus Czinger 21C - the 3D printed hypercar
A decade ago, the idea of 3D printing a car would have seemed like an outlandish idea. In 2023, it is very much a reality thanks to the efforts of Czinger, the California-based manufacturer of the 21C, a 1300hp+ hybrid hypercar that makes extensive use of additive manufacturing (AM) technology across both its chassis and engine.
Czinger is an offshoot of Divergent 3D, a company looking to disrupt the automotive manufacturing industry with its DAPS (Divergent Adaptive Production System) concept. Intended to be a complete software and hardware solution for tool-less manufacturing, leaning heavily on generative design processes and AM, company founder Kevin Czinger’s vision is that DAPS can replace the traditional vehicle production process.
Czinger is an offshoot of Divergent 3D, a company looking to disrupt the automotive manufacturing industry with its DAPS (Divergent Adaptive Production System) concept. Intended to be a complete software and hardware solution for tool-less manufacturing, leaning heavily on generative design processes and AM, company founder Kevin Czinger’s vision is that DAPS can replace the traditional vehicle production process.
As Ewan Baldry, Czinger’s chief engineer, explains, the purpose of the 21C initially was to be a technology demonstrator for Divergent’s technology. Originally called the Blade, the car was “an in-house project to practice and develop the techniques, that would produce something marketable to demonstrate the technology”, Baldry says. The project served this purpose well and Divergent now has several OEM customers. However, a private showing of the car at the Pebble Beach Concours d’Elegance in 2019 sparked such a positive reaction that the project morphed from a concept into a bonafide, homologated production car, and the Czinger brand was created.
Baldry’s background is firmly track based. Though he started his career at Rolls-Royce then TVR, followed by a stint at Williams F1, he is best known for founding Juno Racing Cars, a producer of highly acclaimed Sports 2000 and Formula Ford racers. Juno was acquired by Ginetta Cars in 2014, where he became technical director until his move to Divergent in 2018.
Unsurprisingly, his team at Czinger has a strong motorsport pedigree, but balanced with the expertise needed to bring an engine with all the traits of a racing unit to the road. For example, director of powertrain Jim Maher lists former employers such as Cosworth and Integral Powertrain on his CV, and in recent years Aston Martin and Bosch, where he headed the company’s UK engineering department for automotive powertrain applications.
Baldry’s background is firmly track based. Though he started his career at Rolls-Royce then TVR, followed by a stint at Williams F1, he is best known for founding Juno Racing Cars, a producer of highly acclaimed Sports 2000 and Formula Ford racers. Juno was acquired by Ginetta Cars in 2014, where he became technical director until his move to Divergent in 2018.
Unsurprisingly, his team at Czinger has a strong motorsport pedigree, but balanced with the expertise needed to bring an engine with all the traits of a racing unit to the road. For example, director of powertrain Jim Maher lists former employers such as Cosworth and Integral Powertrain on his CV, and in recent years Aston Martin and Bosch, where he headed the company’s UK engineering department for automotive powertrain applications.
Meanwhile, Chris Wright, in charge of powertrain performance, arrived from Formula 1 having spent six years with Honda before which he worked at both Cosworth and Mercedes AMG HPP as well as Zytek (now Gibson). Powertrain technical program manager Luiz Oliveira also hails from Mercedes’s Brackley F1 operation, before which he worked on Honda Performance Development’s IndyCar program.
Hybrid punch
The 21C’s V8, capable of running on either gasoline or ethanol, is fed by twin-turbochargers and mates to a 7-speed sequential transmission with internals developed by Xtrac. The over square engine has a bore and stroke of 84x65mm, befitting its high-rpm nature. The valve train is relatively conventional, with variable valve timing on the inlet and a combination chain and gear drive operating four valves per cylinder via quad cams, acting directly on shimmed bucket lifters with traditional valve springs. The ICE’s output is augmented by three MGUs (motor generator units), a 150kW unit mated directly via a geared drive to the engine’s crank, and two, 200kW units on the front axle, sending drive to the wheels via reduction gearbox (at a 5.95:1 ratio).
Unusually, the flat plane crank engine has an 80° bank angle, one of several architecture choices made due to the very tight packaging constraints imposed by the chassis layout. As Baldry explains, “One of the key drivers for the powertrain architecture was the unique layout of the car, in particular the in-line seating. This is packaged within a typical wheelbase dimension and so obviously requires a very compact combustion engine and rear transmission assembly.” This was also the key driver for developing an engine in-house. “There simply wasn’t anything in existence that could deliver what we needed and so we had to set about creating our own,” he notes.
With this packaging challenge led to the unusual choice of vee angle, as Maher says: “It just narrows the vehicle very slightly. That 10° change in angle saves us a significant amount of width from the engine, without increasing the height too much due to the size and shape of the cylinder heads.” The layout does necessitate an odd firing order, but Maher asserts the impact of the resulting vibrations is negligible and, as a happy offshoot, gives a unique engine note.
The 21C’s V8, capable of running on either gasoline or ethanol, is fed by twin-turbochargers and mates to a 7-speed sequential transmission with internals developed by Xtrac. The over square engine has a bore and stroke of 84x65mm, befitting its high-rpm nature. The valve train is relatively conventional, with variable valve timing on the inlet and a combination chain and gear drive operating four valves per cylinder via quad cams, acting directly on shimmed bucket lifters with traditional valve springs. The ICE’s output is augmented by three MGUs (motor generator units), a 150kW unit mated directly via a geared drive to the engine’s crank, and two, 200kW units on the front axle, sending drive to the wheels via reduction gearbox (at a 5.95:1 ratio).
Unusually, the flat plane crank engine has an 80° bank angle, one of several architecture choices made due to the very tight packaging constraints imposed by the chassis layout. As Baldry explains, “One of the key drivers for the powertrain architecture was the unique layout of the car, in particular the in-line seating. This is packaged within a typical wheelbase dimension and so obviously requires a very compact combustion engine and rear transmission assembly.” This was also the key driver for developing an engine in-house. “There simply wasn’t anything in existence that could deliver what we needed and so we had to set about creating our own,” he notes.
With this packaging challenge led to the unusual choice of vee angle, as Maher says: “It just narrows the vehicle very slightly. That 10° change in angle saves us a significant amount of width from the engine, without increasing the height too much due to the size and shape of the cylinder heads.” The layout does necessitate an odd firing order, but Maher asserts the impact of the resulting vibrations is negligible and, as a happy offshoot, gives a unique engine note.
Backing up the IC engine is a power dense hybrid system, developed in conjunction with partners Integral Powertrain and RML (Ray Mallock Limited) in the UK. The system runs at 650V and consists of a pair of three-phase radial flux motors on the front axle and a similar, but slightly lower output, unit geared to the crank. Two battery packs are mounted either side of the chassis and utilize a cell chemistry that provides a very high C rate, necessary to cater to the three motors when at full output. This of course compromises energy density, but an acceptable range on all electric is still achievable, though Baldry points out that EV range wasn’t the main reason for hybridizing the 21C.
As to why Czinger chose to drive the crank directly (a P1 layout) with the rear MGU, rather than a takeoff at the clutch or transmission (in a P2 or P3 setup), Maher says, “It’s a position that makes sense because it gives us extra flexibility in how we use it.” The rear MGU can either directly add to the output of the engine or be used to charge the battery, while the front motors can also either recover or deploy energy. Balancing between these various modes creates a plethora of options to maximize either power delivery or recovery.”
As to why Czinger chose to drive the crank directly (a P1 layout) with the rear MGU, rather than a takeoff at the clutch or transmission (in a P2 or P3 setup), Maher says, “It’s a position that makes sense because it gives us extra flexibility in how we use it.” The rear MGU can either directly add to the output of the engine or be used to charge the battery, while the front motors can also either recover or deploy energy. Balancing between these various modes creates a plethora of options to maximize either power delivery or recovery.”
Emissions compliance
Meeting global emissions standards required a two-pronged approach from the team at Czinger; optimizing the ICE while also making best use of its strategies for deploying the hybrid system. Wright highlights, “First of all, with the target output of 950hp from 2.9-liters, we are already significantly downsized, which is an enabler toward reducing emissions. But we are also a hybrid.” Here, the flexibility available from the hybrid layout comes to the fore.
For example, during the all-important warm-up phase for the engine, the car can operate as a range extender, with drive provided only via the front motors. “We can pick our operating points to put heat into the catalysts, but also minimize the emission coming out the engine at the same time. We use electrically heated catalysts, and have plenty of electrical power available, so we preheat the catalysts. That means we can effectively start the car, drive away on the front axle, while we’re preheating the catalysts, then fire the engine and optimize its operating mode to put heat into the catalysts,” says Wright.
Significantly, the engine also relies on port, rather than direct injection, with two injectors per cylinder (with air fed via one plenum per bank with a single throttle body on each). Wright explains, “GDI has been quite popular in recent years as an enabler for downsizing, allowing you to push out the knock limit, full load run a higher compression ratio, get better fuel economy, and also get the performance with turbo charging. We don’t need that and can push our knock limit by running on ethanol.”
Furthermore, the turbocharger setup is optimized for top-end performance as the electric motors can be used for torque fill at lower speeds. “That means we don’t really need to push to really high kind of specific outputs at low engine speeds. So, this again enables us to move to retain the PFI which is a simpler fueling system. But it also has benefits in terms of emissions as GDI engines suffer from emissions in a way that PFI doesn’t. If you have GDI, you have a more complex and expensive fuel injection system, but then you also need to add on additional after treatments, such as a GPF. We don’t need any of that and also get really good fuel preparation which helps with combustion.”
Meeting global emissions standards required a two-pronged approach from the team at Czinger; optimizing the ICE while also making best use of its strategies for deploying the hybrid system. Wright highlights, “First of all, with the target output of 950hp from 2.9-liters, we are already significantly downsized, which is an enabler toward reducing emissions. But we are also a hybrid.” Here, the flexibility available from the hybrid layout comes to the fore.
For example, during the all-important warm-up phase for the engine, the car can operate as a range extender, with drive provided only via the front motors. “We can pick our operating points to put heat into the catalysts, but also minimize the emission coming out the engine at the same time. We use electrically heated catalysts, and have plenty of electrical power available, so we preheat the catalysts. That means we can effectively start the car, drive away on the front axle, while we’re preheating the catalysts, then fire the engine and optimize its operating mode to put heat into the catalysts,” says Wright.
Significantly, the engine also relies on port, rather than direct injection, with two injectors per cylinder (with air fed via one plenum per bank with a single throttle body on each). Wright explains, “GDI has been quite popular in recent years as an enabler for downsizing, allowing you to push out the knock limit, full load run a higher compression ratio, get better fuel economy, and also get the performance with turbo charging. We don’t need that and can push our knock limit by running on ethanol.”
Furthermore, the turbocharger setup is optimized for top-end performance as the electric motors can be used for torque fill at lower speeds. “That means we don’t really need to push to really high kind of specific outputs at low engine speeds. So, this again enables us to move to retain the PFI which is a simpler fueling system. But it also has benefits in terms of emissions as GDI engines suffer from emissions in a way that PFI doesn’t. If you have GDI, you have a more complex and expensive fuel injection system, but then you also need to add on additional after treatments, such as a GPF. We don’t need any of that and also get really good fuel preparation which helps with combustion.”
AI dreams
The tandem seating position meant not only did the engine have to be as short as possible, so too did the gearbox. Here, working in conjunction with Xtrac, the team at Czinger has developed an exceptionally compact transmission that heavily utilizes Divergent’s expertise in AM and topology optimization. “It’s not just a 3D printed version of a cast transmission, it is designed from scratch in our unique way,” states Maher. The resulting unit has the trademark organic shape that results from topology optimization, and blends seamlessly into the rear chassis structure, which is also an AM part.
The transmission is currently the most significant part of the powertrain to be additive manufactured, with the majority of ‘bolt on’ parts also produced in this way. However, as Maher points out, parts are not just 3D printed for the sake of it: “We apply the techniques and tools we have access to at Divergent, where we think they’re appropriate. It just so happens, the more you do that, the more you spot opportunities. Parts that in the past were maybe fabricated or machined, we’re just naturally moving to using our in-house tools, because they’re better and give us more options.”
In fact, Baldry suggests that the 21C’s design would have been almost impossible to realize without Divergent’s particular skill set. “The wild shapes and profiles aren’t just to look cool, they are the result of dealing with the packaging challenges we have. It has this skeletal, bone like structure both from a materials efficiency point of view, but also to navigate around tricky load paths with things like the powertrain in the way. We’re able to kind of deal with the challenges of the layout with this technology that’s available to us,” he says.
The tandem seating position meant not only did the engine have to be as short as possible, so too did the gearbox. Here, working in conjunction with Xtrac, the team at Czinger has developed an exceptionally compact transmission that heavily utilizes Divergent’s expertise in AM and topology optimization. “It’s not just a 3D printed version of a cast transmission, it is designed from scratch in our unique way,” states Maher. The resulting unit has the trademark organic shape that results from topology optimization, and blends seamlessly into the rear chassis structure, which is also an AM part.
The transmission is currently the most significant part of the powertrain to be additive manufactured, with the majority of ‘bolt on’ parts also produced in this way. However, as Maher points out, parts are not just 3D printed for the sake of it: “We apply the techniques and tools we have access to at Divergent, where we think they’re appropriate. It just so happens, the more you do that, the more you spot opportunities. Parts that in the past were maybe fabricated or machined, we’re just naturally moving to using our in-house tools, because they’re better and give us more options.”
In fact, Baldry suggests that the 21C’s design would have been almost impossible to realize without Divergent’s particular skill set. “The wild shapes and profiles aren’t just to look cool, they are the result of dealing with the packaging challenges we have. It has this skeletal, bone like structure both from a materials efficiency point of view, but also to navigate around tricky load paths with things like the powertrain in the way. We’re able to kind of deal with the challenges of the layout with this technology that’s available to us,” he says.
The 21C certainly places a spotlight on Czinger’s novel approach to vehicle manufacture. With several performance milestones ticked using the current VP1.2 prototypes (including setting a lap record around the Laguna Seca racetrack), development of the production intent VP2.0 cars is well underway including further evolution of the powertrain. Work is also advanced on greater use of AM parts, and Baldry reveals that there are plans to deploy a printed block in the near future, further demonstrating the technology’s ever-growing potential.
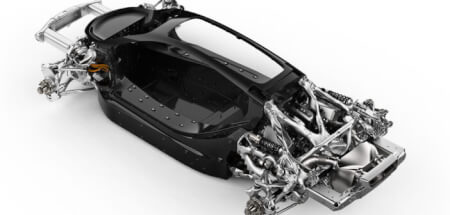